摘 要: 隨著電子技術(shù)的蓬勃發(fā)展,撓性印制電路板的線路節(jié)距正在不斷減小。當(dāng)常規(guī)設(shè)備批量生產(chǎn)線寬/線距為0.05mm/0.05mm的精細(xì)導(dǎo)線圖形時(shí),其合格率也并未因生產(chǎn)條件受到嚴(yán)格控制而得到提高。
本文結(jié)合實(shí)際闡述了具有自動(dòng)化程度高、生產(chǎn)效率、合格率高的Roll to Roll生產(chǎn)工藝,并采用Roll to Roll生產(chǎn)工藝對(duì)精細(xì)線路進(jìn)行了研制。
一、Roll to Roll生產(chǎn)工藝的出現(xiàn)
1898年,英國(guó)專(zhuān)利中首次在世界上提出了石蠟紙基板中制作扁平導(dǎo)體電路的發(fā)明,幾年后,大發(fā)明家愛(ài)迪生也在實(shí)驗(yàn)記錄中大膽地設(shè)想了在類(lèi)似薄膜上印刷厚膜電路。然而直到20世紀(jì)70年代初,隨著聚酰亞胺樹(shù)脂合成的工業(yè)化,美國(guó)PCB業(yè)才率先將FPC工業(yè)商品化,使得其在軍工電子產(chǎn)品中得到使用。隨后,用于FPC制造的FCCL也伴同PI薄膜產(chǎn)品的發(fā)展走上先進(jìn)規(guī)模的工業(yè)化道路,F(xiàn)PC的制造逐漸在各國(guó)PCB業(yè)迎來(lái)春天,以其輕、薄、短、小、結(jié)構(gòu)靈活的特點(diǎn)牢牢吸引住了各類(lèi)電子設(shè)備生產(chǎn)商的眼光。
隨著FPC產(chǎn)品的廣泛應(yīng)用,產(chǎn)品對(duì)制作技術(shù)的要求日趨提高,片式生產(chǎn)技術(shù)已不能滿(mǎn)足部分產(chǎn)品的技術(shù)需求,尤其是當(dāng)常規(guī)設(shè)備批量生產(chǎn)線寬/線距為0.05mm/0.05mm的精細(xì)導(dǎo)線圖形時(shí),其合格率也并未因生產(chǎn)條件受到嚴(yán)格控制而得到提高。針對(duì)片式生產(chǎn)技術(shù)的費(fèi)時(shí)費(fèi)力、勞動(dòng)強(qiáng)度大、生產(chǎn)率低、尺寸穩(wěn)定性(受熱、受濕)較難保證,以及對(duì)于制造高密度精細(xì)線寬/線距的FPC合格率不高,質(zhì)量亦難保證,而開(kāi)發(fā)的連續(xù)傳送滾筒(Roll to Roll)生產(chǎn)工藝便成功地解決了上述問(wèn)題。
20世紀(jì)80年代,世界上少數(shù)大型
FPC生產(chǎn)廠家就開(kāi)始建立了RTR生產(chǎn)線,由于當(dāng)時(shí)所采用的工藝技術(shù)尚未成熟,使得RTR生產(chǎn)線上所生產(chǎn)的FPC產(chǎn)品合格率仍然很低。
90年代后期,日本、歐美的連續(xù)卷帶法生產(chǎn)FPC在生產(chǎn)工藝、設(shè)備上都有了很大的進(jìn)展。特別是21世紀(jì)初,RTR方式生產(chǎn)FPC的技術(shù)的發(fā)展更體現(xiàn)在了FPC產(chǎn)品制造寬度、高密度布線、孔加工方式、雙面板制作上。
二、Roll to Roll生產(chǎn)工藝的特點(diǎn)
RTR技術(shù)是指撓性覆銅板通過(guò)成卷連續(xù)的方式進(jìn)行FPC制作的工藝技術(shù)。采用Roll-to-Roll生產(chǎn)工藝,不僅能提高生產(chǎn)率,而更重要的是提高自動(dòng)化程度。這種高自動(dòng)化的生產(chǎn)明顯地減少了人為操作和管理因素,受環(huán)境條件(溫度、濕度潔凈度等)影響變化小,因而具有更均勻一致而穩(wěn)定的尺寸偏差,從而也易于進(jìn)行修正和補(bǔ)償,所以它具有更高的產(chǎn)品合格率、質(zhì)量和可靠性。
三、Roll to Roll生產(chǎn)工藝的應(yīng)用
我國(guó)由于FPC起步較晚,RTR制作技術(shù)應(yīng)用較少。為了迎合FPC產(chǎn)品市場(chǎng)的需要,提升市場(chǎng)競(jìng)爭(zhēng)力,國(guó)內(nèi)撓性印制板生產(chǎn)企業(yè)也紛紛把目光投入RTR生產(chǎn)技術(shù),開(kāi)始進(jìn)行“RTR撓性電路開(kāi)發(fā)與應(yīng)用”的研究。為達(dá)到高精細(xì)線路制作的高良品率和低成本化的工藝水平,我司也于2007年投入到Rol to Roll工藝生產(chǎn)撓性印制板的應(yīng)用與研究中,旨在解決片式生產(chǎn)高精密線路開(kāi)短路嚴(yán)重合格率低的問(wèn)題,同時(shí)達(dá)到減少人力成本的目的。本文即通過(guò)本司在RTR方式生產(chǎn)FPC板的技術(shù)改造對(duì)“RTR FPC開(kāi)發(fā)與應(yīng)用”進(jìn)行闡述。
3.1 流程確定
RTR方式生產(chǎn)FPC的技術(shù)改造,首先應(yīng)根據(jù)RTR設(shè)備的性能及企業(yè)實(shí)際生產(chǎn)的FPC產(chǎn)品類(lèi)型和特點(diǎn)的需要確定整個(gè)流程如何分段,或顯影、蝕刻、脫膜、后處理一體,或顯影與蝕刻、脫膜、后處理分離。顯影與蝕刻分離的作用,在于分離后顯影線與蝕刻線可同時(shí)進(jìn)行不同底銅厚度的FPC的生產(chǎn),可獨(dú)立調(diào)節(jié)顯影線和蝕刻線的參數(shù)多樣生產(chǎn)??紤]到我司1/2oz、1oz底銅使用量都很大的情況最終采用的是分段式(蝕刻與顯影分開(kāi))雙列250mm寬DES線。
3.2 RTR工藝生產(chǎn)FPC的研究
在確定對(duì)RTR如何分段后, RTR的定位方式、張力控制、傳送控制和材料彎曲變形的防止四因素便成了關(guān)鍵。
上世紀(jì)80年代,RTR生產(chǎn)線所生產(chǎn)FPC產(chǎn)品的合格率低很大程度上也就正是因?yàn)檫@些技術(shù)尚未成熟完善。各工序中定位和張力、傳送控制都與材料平整度的保持直接聯(lián)系,不恰當(dāng)?shù)亩ㄎ环绞?、傳送參?shù)以及放收卷時(shí)不適宜的張力都會(huì)引起材料的彎曲變形。為實(shí)現(xiàn)RTR生產(chǎn)工藝的優(yōu)勢(shì),需對(duì)各工序的張力、傳送等因素進(jìn)行調(diào)整和嚴(yán)格的控制。以下通過(guò)線寬/線距為0.05mm/0.05mm的精細(xì)線路的研制分別介紹。
3.2.1 選材
高精細(xì)線路的制作中,制作方式非常重要,基材的選取也相當(dāng)關(guān)鍵。根據(jù)以往在制作高精細(xì)線路時(shí)的經(jīng)驗(yàn),減成法制備精細(xì)線路時(shí),底銅厚度越薄越易達(dá)到預(yù)想效果,制備出線寬損失小,蝕刻系數(shù)大,側(cè)蝕程度小的線路。片式生產(chǎn)中當(dāng)基材厚度較薄時(shí),為防止在開(kāi)料到壓制前操作導(dǎo)致的褶皺,常規(guī)的方法是在基材上先貼背膠,而RTR設(shè)備生產(chǎn)則不存在這一問(wèn)題無(wú)需背膠。
3.2.2 貼膜
貼膜是撓性印制板圖形轉(zhuǎn)移的第一步,貼膜品質(zhì)直接影響整個(gè)圖形轉(zhuǎn)移的成敗。高品質(zhì)的貼膜不僅要杜絕因銅面和干膜的不潔引起的板面雜質(zhì),而且板面要求平整、無(wú)氣泡、無(wú)皺折,干膜的附著力達(dá)標(biāo),密合度高。對(duì)于全自動(dòng)卷式生產(chǎn),貼膜工序各參數(shù)的控制就更為重要,稍有不慎,造成的浪費(fèi)損失將是巨大的。
雖然RTR設(shè)備生產(chǎn)FPC不需背膠解決薄板的褶皺問(wèn)題,但各工序中仍然要十分注意操作過(guò)程中的傳送和張力控制防止材料的彎曲變形。貼膜工序中則重點(diǎn)控制好貼膜的壓力、溫度和卷材傳送的速度,避免不當(dāng)溫度、傳送速度造成的針孔、氣泡和皺折,使得銅面干膜附著力高。
3.2.3 曝光
曝光是撓性印制板線路形成的開(kāi)始。精確對(duì)位、曝光能量是曝光工序中需特別注意的因素,其中對(duì)位精度在RTR自動(dòng)曝光流程中尤為重要,一旦對(duì)位出現(xiàn)偏差而進(jìn)行返工,將造成整卷干膜等資源的浪費(fèi)。
近年來(lái),不斷有空間對(duì)位方面的發(fā)明出現(xiàn),在我們最新的RTR平行曝光機(jī)中就自帶有尋邊器感應(yīng)卷材傳送以及步距控制器調(diào)控對(duì)位精度,以確保曝光工序線路的形成。
3.2.4 DES
曝光完成后,撓性印制板的圖形轉(zhuǎn)移便進(jìn)入濕流程階段。卷式流程與片式流程的DES工序并沒(méi)有太大的變化,主要區(qū)別在于卷式流程中由于薄基材未貼壓背膠,卷材在DES的傳送過(guò)程中傳送滾輪將有可能在線路面上造成行輪印,影響導(dǎo)體的外觀及性能。為避免行輪印問(wèn)題的出現(xiàn),可選擇性地將DES線的傳送滾輪替換成實(shí)心滾輪。
3.2.5 與片式生產(chǎn)工藝的比較
比較片式與卷式工藝生產(chǎn)0.05/0.05mm線寬/線距的結(jié)果。
RTR工藝生產(chǎn)的線路的線寬情況和蝕刻系數(shù)都與片式相當(dāng)。然而盡管片式工藝生產(chǎn)0.05/0.05mm線路時(shí)嚴(yán)格控制生產(chǎn)條件,最優(yōu)化工藝參數(shù),其線路的開(kāi)短路仍然大量存在,使得產(chǎn)品合格率不高,最佳批量生產(chǎn)合格率也只達(dá)75%。而采用RTR生產(chǎn)工藝時(shí),由于其減少了人為操作和管理因素,受環(huán)境條件影響變化小,開(kāi)短路問(wèn)題得到了很好的控制,批量生產(chǎn)合格率達(dá)到了90%。
與片式生產(chǎn)工藝相比,RTR生產(chǎn)工藝優(yōu)勢(shì)不僅在于提高了合格率,還體現(xiàn)在大大提高了生產(chǎn)的自動(dòng)化程度。從貼膜曝光到顯影蝕刻脫膜,片式生產(chǎn)需12名操作人員,而RTR生產(chǎn)只需4人,大大的節(jié)省了勞動(dòng)力。
3.3 線寬/線距為0.03mm/0.03mm的精細(xì)線路的研制
3.3.1 選材
眾所周知,F(xiàn)CCL銅箔的厚度越薄,蝕刻后線條的側(cè)蝕越小,尤其是在制備高精細(xì)線路時(shí)。比較了12μm和10μm兩種厚度底銅的覆銅板在制備精細(xì)線路上的優(yōu)劣,筆者最終選用底銅為10μm的2L FCCL作為研制線寬/線距為0.03mm/0.03mm的精細(xì)線路的基材。
精細(xì)線路的研制,所采用干膜的性能也相當(dāng)關(guān)鍵??紤]到在實(shí)際運(yùn)用中同系列干膜的厚度越薄其賦形性能解像能力越佳,在線寬/線距達(dá)到0.03mm/0.03mm精細(xì)線路的研制中將采用15μm厚度的杜邦干膜。
3.3.2 試制
在貼膜過(guò)程中,由于為提高解像度使用了15μm的干膜,其較常用干膜薄50%,故而對(duì)貼膜參數(shù)作了輕微調(diào)整,適量降低貼膜溫度和壓力,加快貼膜速度。曝光過(guò)程,經(jīng)試驗(yàn)證明,對(duì)制作0.03mm線寬線距的精細(xì)導(dǎo)線時(shí),最佳曝光級(jí)數(shù)為6級(jí)(21級(jí)曝光尺)。0.03mm的線寬無(wú)疑是對(duì)RTRDES線制程能力的重大挑戰(zhàn),故在DES過(guò)程中對(duì)顯影蝕刻機(jī)的各參數(shù)調(diào)節(jié)應(yīng)相當(dāng)謹(jǐn)慎。本試制中,為達(dá)到預(yù)期的效果,對(duì)顯影蝕刻機(jī)的運(yùn)行速度與噴淋壓力進(jìn)行了嚴(yán)格的控制。
0.03mm/0.03mm線路的生產(chǎn),確實(shí)很難由片式工藝逾越,而采用在合格率、受環(huán)境影響小等較優(yōu)的RTR技術(shù)其結(jié)果亦不甚讓人滿(mǎn)意,線路的開(kāi)短路雖不嚴(yán)重,但DES的蝕刻速度仍然過(guò)快,所得線路間距跟預(yù)期比過(guò)大。
四、結(jié)束語(yǔ)
目前國(guó)內(nèi)采用減成法制作0.03mm/0.03mm線寬/線距精密線路仍然是PCB業(yè)界的技術(shù)難題。盡管如此,RTR生產(chǎn)工藝的出現(xiàn)大大提高了FPC的生產(chǎn)效率,保證了精細(xì)線寬/線距FPC的合格率,其不僅可應(yīng)用于FPC的生產(chǎn),也可應(yīng)用于FPC后續(xù)的封裝。
隨著電子機(jī)械技術(shù)地不斷發(fā)展,較精密較復(fù)雜的封裝及檢測(cè)儀器(如
自動(dòng)光學(xué)檢測(cè)AOI、雙向非平面軟板錫膏印刷機(jī))亦不斷地被引入到RTR生產(chǎn)線中,日本的Epson等公司已然擁有從
FPC基材形成到最終封裝完畢的全RTR生產(chǎn)線。基于這些優(yōu)點(diǎn),RTR生產(chǎn)工藝的應(yīng)用前景是相當(dāng)廣闊的。
深圳宏力捷推薦服務(wù):PCB設(shè)計(jì)打樣 | PCB抄板打樣 | PCB打樣&批量生產(chǎn) | PCBA代工代料
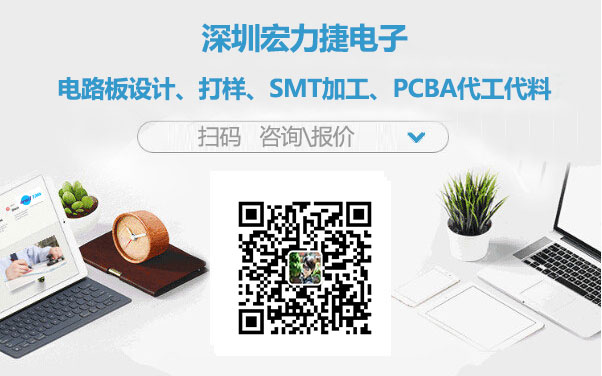